Injecting Safety Innovation and Culture at Waste Pro, a Fast-Growing Waste Management Leader
A partnership with AXA XL and StrongArm Technologies brings actionable safety data to seven high-volume facilities over eight months.
In April of 2021, leading safety wearables company StrongArm Technologies and AXA XL, the commercial insurance and specialty risk division of global insurer AXA, partnered to deploy proactive safety technology and data to one of their most forward-looking insureds: Waste Pro USA, one of the country’s fastest-growing waste management companies.
This three-way partnership came together to protect a critical workforce in our country, and drive on-body safety data analysis into the workers’ compensation space.
After eight months at seven participating facilities, the program’s goal was realized: Use actionable safety data gathered through StrongArm’s Fuse V5 Sensors to dramatically reduce the the potential of risk and injury where it was needed most, and inject an enduring safety culture into a company working at the forefront of our national critical infrastructure.
Program Origins
AXA XL seeks technology partners who share their vision of protecting their clients’ people, projects and profits. In partnering with StrongArm, they help their clients invest in the safety and wellbeing of their most valuable assets — their people — through its leading-edge safety technology fueled by the world’s largest industrial data set.
According to Rick Burggraf, head of strategy, data analytics and technology for AXA XL’s Primary Casualty Insurance business, “Supporting our customers’ technology adoption and innovation efforts by curating technology partners who provide risk-reducing solutions will not only help our clients elevate their loss prevention efforts but will also help pioneer the ‘next generation’ of risk management.”
In this vein, Waste Pro was a natural fit.
Florida-based Waste Pro employs thousands of hardworking Industrial Athletes™ across more than 80 locations, all aligned under the mission to transform the waste and recycling industries into a value-driven service.
Inevitably, in such a fast-moving company with relentlessly high demand, the risk of injury is a persistent threat, despite a deeply ingrained culture of employee health, safety and wellbeing.
For Waste Pro, investing in workplace safety technology was a no-brainer: They’ve always had the will to do right by their staff, they simply needed an actionable benchmark of safety data to bring that to the next level. Adopting StrongArm’s SafeWork System — an integrated system of safety sensors, smart docking stations and data analysis and intervention — was just the solution they were looking for.
The Power of Facility Buy-In
Waste Pro began by integrating StrongArm’s sensors and risk management platform into seven high-volume facilities across the nation — each a vibrant hub of activity with workers, machinery and vehicles whirring at a dizzying pace. With workers across various job types wearing StrongArm safety sensors and collecting ergonomic data in real time, a heat map of real and potential risk began to materialize.
To most effectively identify where injuries might occur and intervene at the source, wholesale adoption spanning job functions — drivers, helpers, recycle, residential, front load, etc. — became critical. Waste Pro adopted StrongArm’s leading safety technology to help better understand where injuries were occurring so they could combat them at the source.
Not surprisingly, a trend emerged in consistency of use: The facilities with the most cumulative checkouts (meaning the most Industrial Athletes™ wearing the sensor every day consistently) saw the greatest reduction in risk potential.
“The health and safety of our employees and the communities they serve will always be a top priority stemming from our CEO to the field. The addition of StrongArm into our safety toolbox has been well received by our insurer and our employees,” says Waste Pro Safety Director Romeo Vellutini. “The StrongArm team was highly responsive throughout our roll out process and addressed any concerns making this an easy tool to implement throughout the Waste Pro footprint.”
Since the program’s onset, Waste Pro has nearly doubled the number of participants in the program, seeing over 8,000 individual checkouts and some 41,000 hours of highly specified safety data. Daytona Beach, in particular, has been a standout participant in this program to date.
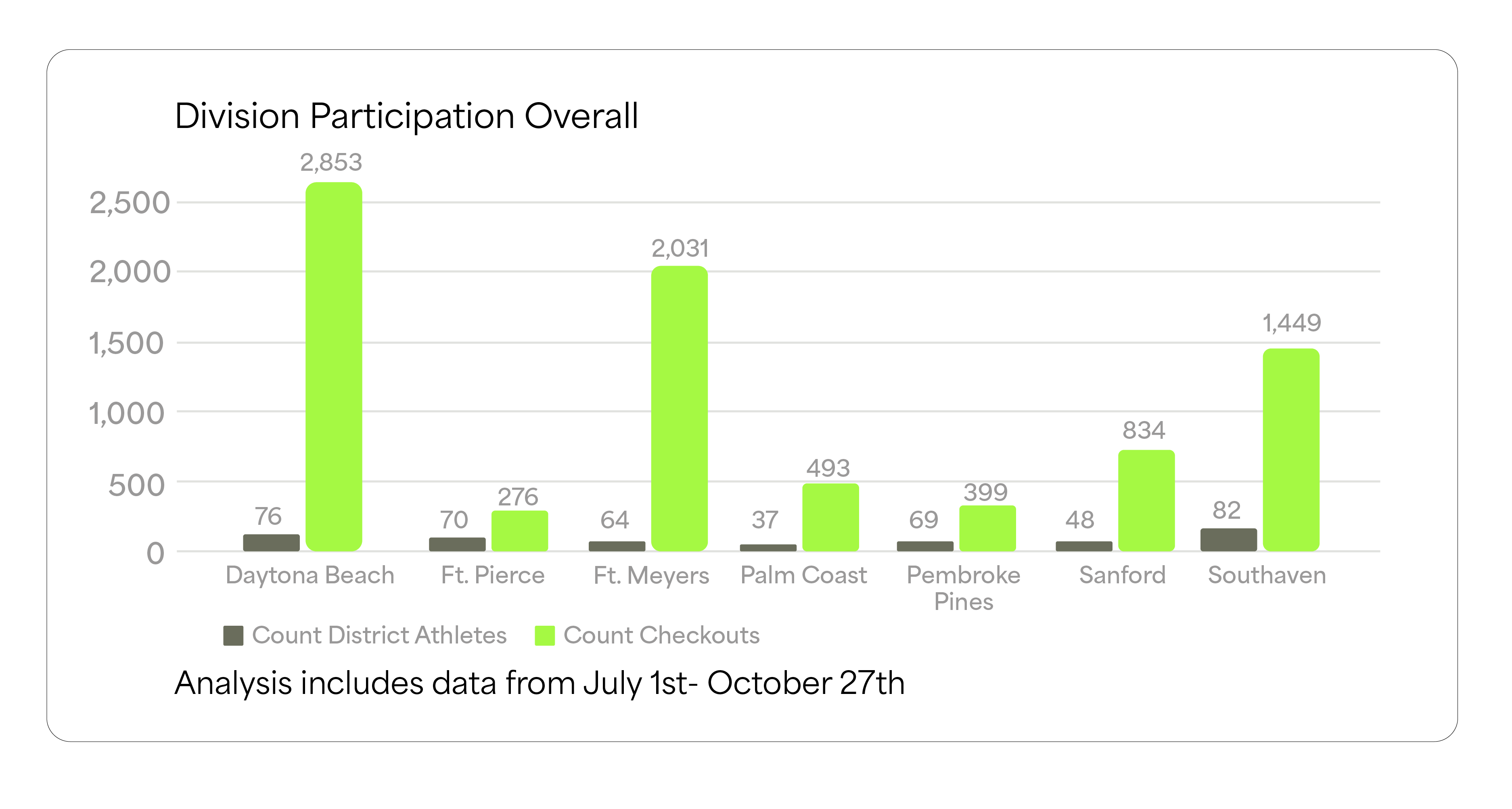
Real-Time Alerts Drive Injury Reduction
For the fast-moving workers at Waste Pro, on-body safety alerts drove real injury reduction, quickly.
An immediate advantage of deploying wearable sensors is the potential to realize positive behavior change in a short period of time, primarily through haptic, or vibrational, feedback. If a worker is bending forward in an ergonomically unsafe way, for example, the Fuse V5 Sensor will buzz — a discrete but tangible indication that the movement is unsafe and should be remedied.
On-body alerts then roll up to an individual’s daily Safety Score, StrongArm’s proprietary numerical ranking from 1-100 for a worker’s daily safety.
When the program began, Waste Pro had an aggregate baseline Safety Score of 59.9 across 300 Industrial Athletes — far below their target working Safety Score of 70 or more.
However, weekly safety reports allowed management to analyze trends in haptic feedback, identifying a wide range in Safety Scores (as high as 78 to as low as 50) and one particular job function, Delivery Helpers, as notably high risk.
Those insights drove clear and actionable intervention methods as a result. Through eight months of monitoring and intervention, we worked with Waste Pro management to successfully shift a downward Safety Score trend, rooted in poor forward bend angles, in the right direction.
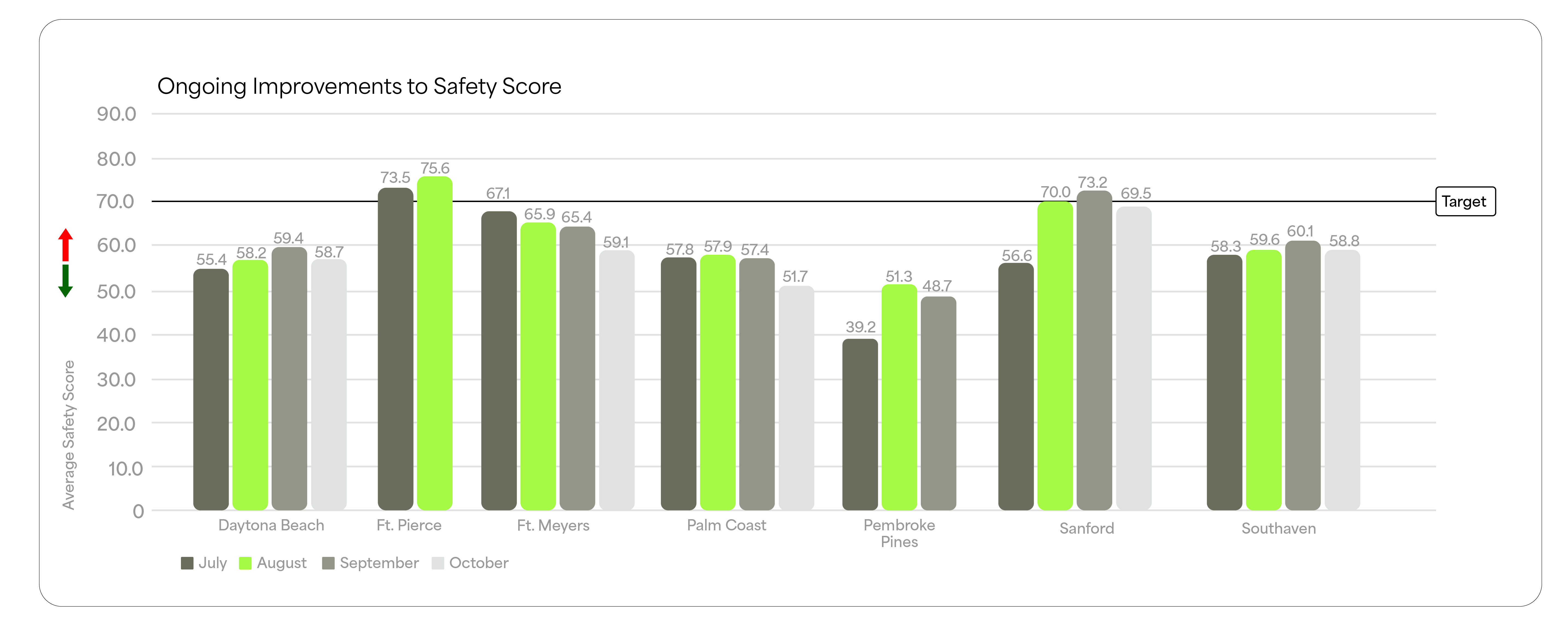
Cultivating a Culture of Safety and Wellness
Waste Pro has a deep culture of promoting worker safety and wellbeing, beginning with morning staff stretches and rolling up to regular and transparent “Safety Bit” checks on sensor data, employee adoption trends and possible intervention opportunities.
It’s a top-down approach to Industrial Athlete safety that translates to happier, healthier and more productive people.
And while the program with StrongArm has been running for less than a year, the results have reverberated across the participating facilities and proven the power of rooting a company’s safety program in actionable safety data.
“StrongArm’s haptic feedback provided to the wearer helps them focus better on proper ergonomics allowing for subconscious correction to form new habits with correct, safe ergonomic movement,” adds Vellutini. “The comprehensive analytics provided to our team allow for our managers to provide customized coaching and the ability to reward employees who are improving and/or utilizing proper ergonomics.”